The science behind reflective trim: tested for the toughest conditions
It starts with science and ends with safety.
When visibility stands between risk and safety, there’s no room for shortcuts. That makes reflective trim more than just an addition to protective gear; it’s a life-critical technology.
At Safe Reflections, performance starts with purpose and is built through science. Every reflective trim we produce is developed with one goal in mind: to deliver reliable, high-visibility performance in the most demanding environments.
From the molecular structure of our materials to the stress protocols in our in-house lab, our trims are engineered to exceed regulatory benchmarks and maintain integrity under repeated exposure to heat, abrasion, and wear.
Whether integrated into firefighting gear, high-visibility vests for overnight roadwork, or construction PPE exposed to extreme weather, our materials are built to stay visible — shift after shift, wash after wash, in conditions where visibility can’t be compromised.
This isn’t about meeting compliance norms, but outperforming them — every shift, every wash, every wear.
Reflectivity is a science, not a PPE accessory
Let’s start with the fundamentals. Retroreflective materials redirect light—vehicle headlights, for example—back to its source. This enables reflective trim garments to cut through darkness, distance, and distraction, creating maximum visibility in minimal-light environments.
But maintaining that visibility — across distance, angles, and motion — is where things get complicated. That’s where our science comes in.
Our trims, like AIREX™, utilize advanced glass bead technology that provides multidirectional retro reflectivity. These micro-glass beads are embedded in engineered substrates designed to flex, stretch, and withstand heat, wash cycles, and abrasion. They are constructed to perform even when the garments they are attached to are bent, crumpled, or soaked in sweat or rain. Moreover, everything is engineered to meet or exceed stringent visibility standards such as ANSI/ISEA 107 and EN ISO 20471 — not just when new, but also after real-world wear.
Branding matters, it should not mean compromising on safety. Our Brilliant® Color Reflective line fuses vibrant color visibility with high-performance reflectivity. Because being seen should also mean being distinctive.
Reflective trim in the field: preparing for the unpredictable
Let’s talk about where Safe Reflections trims actually work.
These aren’t lab-focused materials meant for controlled environments. They’re designed for job sites, emergency situations and disaster zones — places where UV, heat, moisture, grime, abrasion, and fire exposure are just part of the job. PPE garments face physical stress, constant movement, repeated exposure to elements that degrade most fabrics fast, not to mention industrial laundering, which can be punishing.
This is why we simulate those environments in our tests — because what survives our lab has to thrive and help people survive in real life.
Step inside the Safe Reflections Lab
As we said, safety starts with science, and the science starts in our Safe Reflections Lab.
SRI Labs, our advanced in-house facility, is more than a testing center, it’s a critical part of our development process. Staffed by a team with deep expertise in reflective and enhanced visibility materials, the lab is equipped to design and conduct specialized tests that mirror real-world performance conditions. This internal capability allows us to validate durability, reflectivity, and compliance with precision, while driving innovation and responding quickly to customer-specific requirements.
This is where we develop, destroy, and redesign. Ideas transform into prototypes, which either make their way onto garments or are sent back to the drawing board. By keeping R&D, testing, and validation under one roof, we control quality, accelerate development, and adapt faster to our partners’ real-world requirements.
That kind of control isn’t optional when your products protect people under arc flashes, on busy highways, or in burning buildings.
From wash cycles to flame resistance, we test it all
Anyone can claim durability, proving it is another matter entirely.
To be honest, calling our processes “testing” is a bit of an undersell. What we do is stress simulation—deliberate, repeated punishment to validate durability, adhesion, reflectivity, and wear resistance. No product is safe until we say it is.
Here’s what that looks like in practice:
Laundering durability
We test for both home and industrial laundering scenarios, simulating up to 100 home wash cycles under AATCC standards and up to 50 industrial cycles under ISO 15797. These aren’t theoretical limits, but our performance baselines.
Each test evaluates whether retro reflectivity stays within regulated limits post-wash. It doesn’t cut if the trim degrades, cracks, or peels under repeated detergent, heat, and tumble cycles.
Abrasion and flex resistance
From construction sites to fire grounds, garments are constantly flexed, scraped, and stretched. Our trims are put through rigorous abrasion tests – like Martindale and Taber tests – which simulate repeated friction and contact with rough surfaces. Then, they’re flexed again and again to test for cracking or delamination, especially critical for performance after months of wear.
For trims used in firefighting, welding, utilities, and oil and gas, heat exposure is a daily reality. That’s why we test to ASTM D6413, the vertical flame test that evaluates how a material responds to open flame.
Our trims are designed to work with FR-rated garments, ensuring that reflectivity doesn’t compromise flame resistance. We also simulate prolonged heat exposure to identify degradation points well before failure.
Chemical resistance and UV durability
Chemical splash? Common. UV degradation? Inevitable — unless you plan for it.
Our testing protocols include prolonged UV chamber exposure, humidity cycling, and chemical immersion to validate optical clarity and adhesion even after exposure to solvents, oils, and weathering, and even after months of wear.
Adhesion and delamination resistance
It’s one thing for a reflective layer to look good fresh out of the factory. It’s another to stay bonded after laundering, flexing, or exposure to sweat and temperature shifts.
Our bonding technologies are validated against hydrolysis, mechanical stress, and heat cycling. Because when the reflective layer starts to peel, so does your compliance.
This rigorous battery of tests isn’t to satisfy the regulators, but the end users. It’s how we know — and prove — that our materials can protect workers where it counts.
Products built for extremes
Every application has its own demands, which is why our trims aren’t one-size-fits-all.
- AIREX™ is breathable, flexible, and designed for high-mobility use — ideal for utility workers, transportation, industrial, construction and road crews where constant heat and sun exposure are major challenges.
- Triple Trim combines retroreflective performance with contrasting color layers, increasing daytime visibility and reinforcing multi-hazard safety — critical in environments where workers need to be seen 24/7.
Each product line undergoes its own test protocol, based on how it will be used. This isn’t just customization, it’s application-specific engineering.
Why in-house testing is a strategic advantage
We don’t outsource testing and compliance. Here’s why:
- Faster innovation cycles: With research, development, and validation under one roof, we go from concept to tested product faster than competitors relying on third-party labs.
- Customization on demand: When our customers need something specific, such as a product that handles tunnel drying, we can simulate and solve it without waiting for outside facilities. This enables us to partner closely with customers to better serve their requirements.
- Continuous improvement: SRI doesn’t like to leave well enough alone, or rest on our laurels, when there’s always a chance for improvement. Our lab isn’t just for development; it’s for feedback. We incorporate field performance data directly into new product iterations. It’s a never-ending search for improved safety in reflective trims.
It’s all about control, accountability, and confidence. When we validate the products, testing, and results ourselves, we know exactly what our products can handle.
Deciphering the standards: what the labels actually mean
There is no shortage of acronyms in our business. But unless you’re fluent in the compliance lexicon, it’s not always clear what those labels actually mean for your gear or your team’s safety.
Here’s a quick breakdown of the most critical certifications and standards that govern https://safereflections.com/sri-labs/regulations/, and what they mean in the real world:
- ANSI/ISEA 107: The U.S. standard for high-visibility garments. It specifies minimum reflectivity, color brightness, and placement of reflective elements. Our trims routinely exceed these benchmarks after repeated laundering and environmental stress.
- EN ISO 20471 is the international visibility standard. It mirrors ANSI/ISEA 107 but includes additional performance requirements for daylight visibility. Safe Reflections trims meet or exceed this standard, validated by both internal and third-party testing.
- NFPA 1970: The comprehensive U.S. standard for firefighter PPE, covering design, performance, and certification requirements, including flame resistance, where ASTM D6413 is used as the test method. Our FR-compatible trims are engineered to meet NFPA 1970 criteria for visibility, heat resistance, and long-term durability.
- ASTM D6413: The vertical flame test determines whether the material continues burning after exposure to flame. Our FR-compatible trims are tested to this standard and designed to maintain flame resistance integrity.
- ISO 15797 Governs industrial laundering durability. Our trims withstand tunnel finishing, chemical detergents, and mechanical agitation without degradation of reflectivity.
- Oeko-Tex® Standard 100: Ensures all materials are free from harmful substances and safe for direct skin contact. All Safe Reflections core products meet this standard.
These certifications aren’t checkboxes, but performance minimums that are our job to go beyond.
Trusted by those who can’t afford failure
You’ll find Safe Reflections trims on garments used in various sectors, because we specifically engineer for them.
- Firefighting and emergency response
- Utilities and energy
- Mining and heavy industry
- Construction and infrastructure
- Defense and public safety
Our partners include top-tier PPE brands and OEMs who rely on our materials because they’re tested, traceable, and trusted. They’re not settling for “good enough.” They need gear that performs on the toughest days, every day, and they rely on a partner who can deliver every time.
From lab to life: a commitment to performance
When we say it starts with science and ends with safety, we mean that every reflective trim we produce has more than just brightness, but countless hours of meticulous engineering, exhaustive testing, and a relentless focus on end-user performance.
We invite safety officers, procurement teams, and PPE designers to look deeper — not just at reflectivity ratings, but at durability under pressure, compliance with evolving standards, and compatibility with the garments your teams rely on.
If your gear needs to work in the toughest conditions, we’ll show you what’s possible.
Explore our product sheets or book a consultation to talk with our materials team. Because safety shouldn’t rely on assumptions — it should be built on science.
If you’re in the process of maximizing the visibility of your first responder teams, bring us your challenges, and Safe Reflections will help you transform them into obvious solutions. Contact us today.
Recent Resources
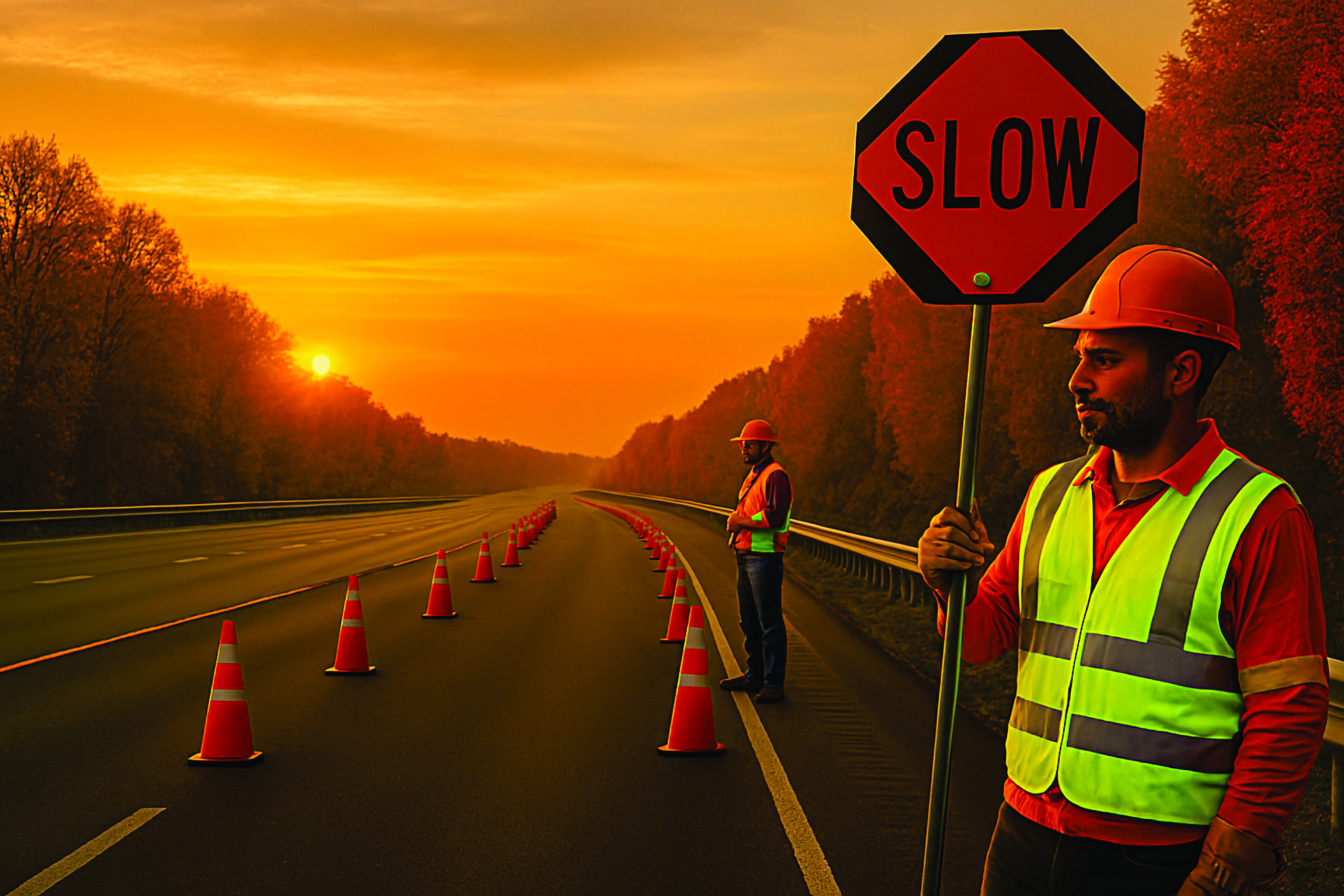
Fading Light and the Need for Reflective Safety
As summer fades, so does the light, making high
–
visibility safety apparel (HVSA) a priority as autumn’s
later
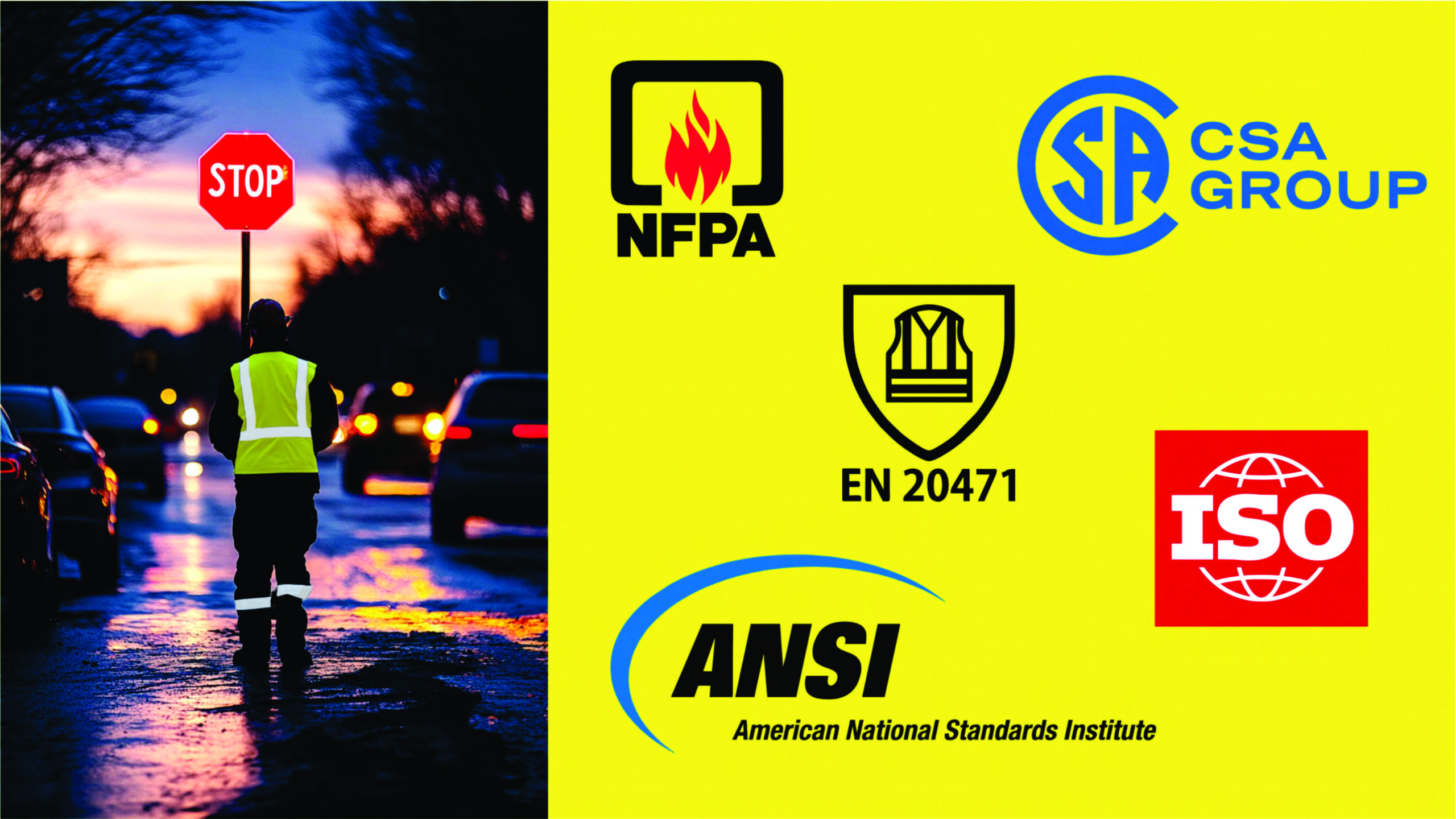
Beyond ANSI: The Real Science Behind High – Visibility Reflective Safety Gear
Regulations aren’t simply bureaucratic red tape, they’re critical guidelines designed to keep workers visible, safe, and protected in high-risk environments.
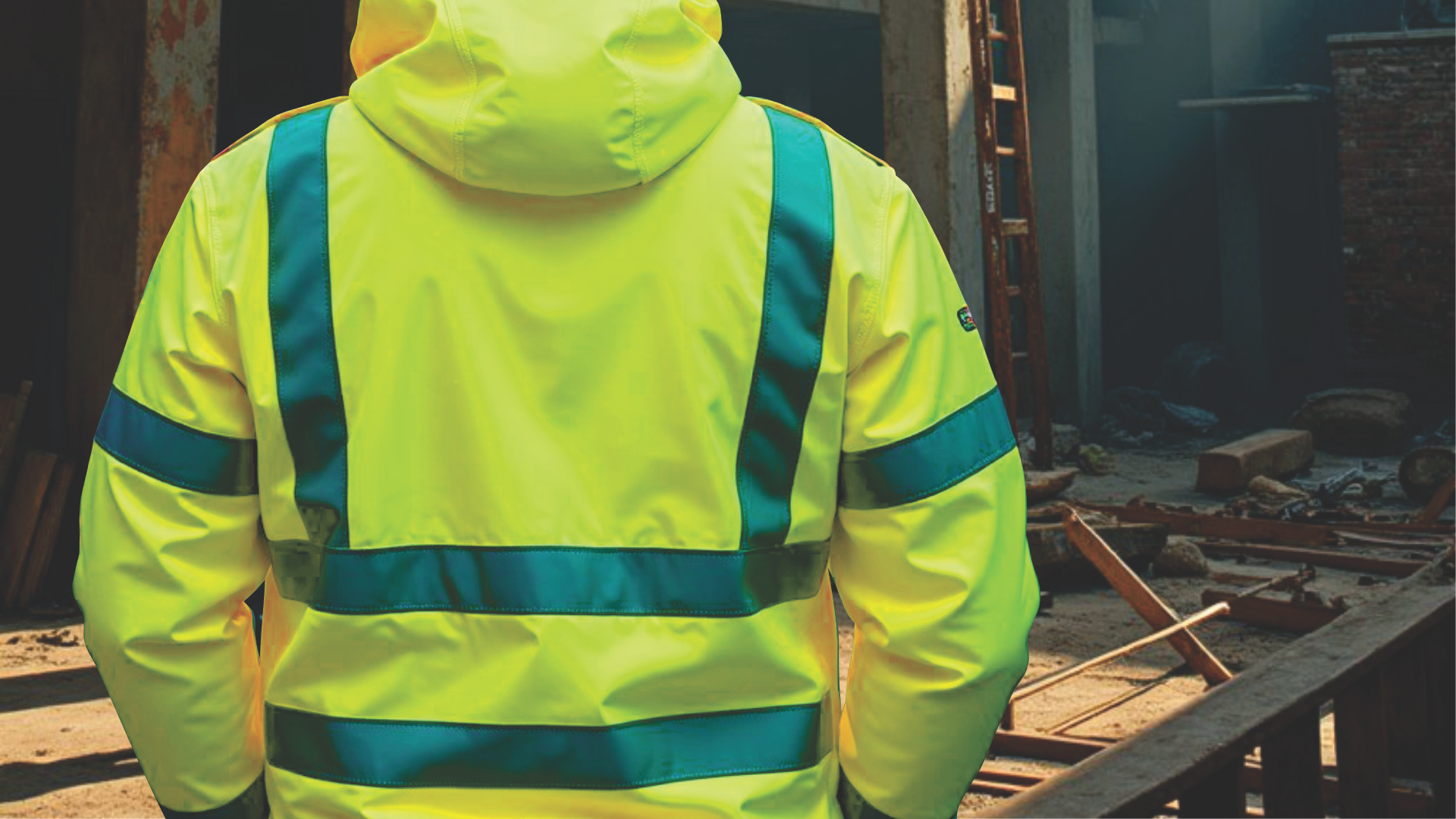
Above and Beyond ANSI
At Safe Reflections, we keep a close eye on reflective visibility standards because we see them as just the starting point for